A GUIDE TO CORRECT USE OF ANTISTATIC FOAMS
History
Pink ESD foam has been ubiquitous in the world of ESD packaging since its inception back in the 1970's. It is a great product that fulfills many requirements in many situations. Pink foam has regularly been used as a cushioning aspect of packaging or work surface and became an "answer” for many ills. There has been some confusion regarding the ant-static nature of the foam and how long it lasts. Pink anti-static foams have a shelf life. Once the shelf life is gone, pink foam can be extremely dangerous sensitive components and the manufacturing environment. Looking closer at an EPA (ESD Protected Area), the using, or misusing these foams is the most commonbroken standard ESD practices.
As it relates to ANSI/ESD S20.20, 6.1 and 6.2 of ANSI/ESD S541 tells us that packaging (in our case, pink foam) used inside and outside an EPA must meet certain characteristics.
6.1 Inside an EPA
Packaging used within an EPA (that satisfies the minimum requirements of ANSI/ESD S20.20) shall be:
- Low charge generation.
- Dissipative or conductive materials for intimate contact.
- Items sensitive to < 100 volts human body model may need additional protection depending on application and program plan requirements.
6.2 Outside an EPA
Transportation of sensitive products outside of an EPA shall require packaging that provides:
- Low charge generation.
- Dissipative or conductive materials for intimate contact.
- A structure that provides electrostatic discharge shielding.
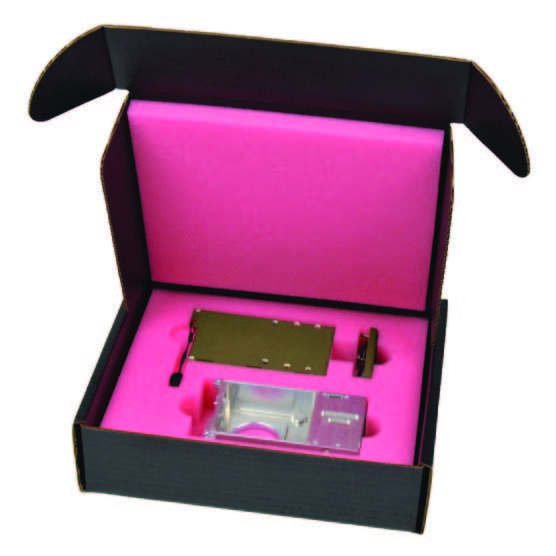
Low charge generation is one of the characteristics of the materials used. S541 also points out that for "intimate" or immediate contact of sensitive products, the packaging must be dissipative or conductive. Foam is used for "intimate contact" in most applications. That is why it's so important to understand what is ESD static dissipative about pink foam and why it has a shelf life. When that shelf life has been exceeded, you're left with regular foam. In order to better understand the “shelf life,” first we need to look at at regular foam in general, ESD foam, and appropriate applications of it.
Foam Is Great For Cushioning
Regular foam offers great cushioning to protect items from physical impact. The problem with regular foam is that it sits very high on the triboelectric scale for producing a static charge. FYI, all materials, including conductors, can be tribo-electrically charged. The level of charge is impacted by type of material, velocity of contact and separation, humidity and several additional factors. As a result, regular (non ESD) foam is cannot be used in an EPA (ESD Protected Area) environment. Remember, once the ESD properties disappear from the Pink ESD Foam, you're left with regular foam.
Pink Anti Static Foam
Considering its high surface area and chemical composition, flexible foam is ideal for the build-up of static charges. This property is overcome by adding anti-static chemical additives or anti-static surfactants. These additives are most commonly added to the foam during the manufacturing process. The color pink is just what the industry chose to help identify the foam as a category of “ESD” or “Antistatic” materials.
The surfactants used are low molecular weight fatty acids typically developed from amides or amines. Surfactants are mobile (blooming) surface modifiers that temporarily change the friction properties between mating surfaces (tribo charging). This is a pretty substantial statement. Let’s break it down to help understand it better. The molecules (in surfactants) in their initial state are unsaturated.
The unsaturated bonds in these molecules want to absorb moisture. In this unsaturated state, they lower the friction of the foam and help in its Antistatic properties. The challenge of unsaturated molecules is they are made to become saturated. Once the molecule is saturated, they are considered expired and their antistatic properties are done. How much time for these molecules to become saturated? That varies depending on a few factors. Humidity and the environment play vital roles.
The handling of the foam plays a vital role. The truth is, there isn't any concrete guideline for how long this takes. Most people in the industry look at one year as the critical date to begin testing and others recommend testing earlier and some later. It all comes down to your understanding and your procedures. What works for some might not work for others.
Shelf Life
So now we know why foam has a shelf life. Once the shelf life has gone, foam will not appear any different, but its ESD protective properties will be gone. We also know that, based on many factors, shelf life can range in timespan. So what to do?
It's a good thing that the ESD Association gives us a guideline to help navigate this problem. 6.1 and 6.2 of ANSI/ESD S541 tells us, as it relates to ANSI/ESD S20.20, that packaging (pink foam) used both inside and outside an EPA must meet certain characteristics. One of these characteristics is that materials must be low charge generating. It also says that for intimate contact of sensitive products, it must be dissipative or conductive.
Foam is usually used for intimate contact of sensitive products. You see it lining racks and shelves, in bottom of drawers, inside boxes and as separators between stacks of circuit boards or assemblies. That’s pretty self-explanatory. We cannot have any charge generating packaging material in an EPA or in specific circumstances outside of an EPA.
But now we have an issue. We've outlined and explained why these foams might or might not be static safe. If the foam still meets its material specifications, we’re all good to go. If the properties of pink foam are gone, what should you do? Luckily for us, we can turn again to the ESD Association for guidance. More specifically, ANSI/ESD S541. In section A.6:
The static control properties of some packaging materials can deteriorate with time and use. Compliance Verification of static control packaging properties should be part of the ESD control compliance verification plan.
A6 Compliance Verification
This is an important statement. It not only validates that material will degrade over time, it also states that we must create a verification process to assure the properties are still present. ESD TR53-01-06 is another refernce to validate this. This document covers compliance verification of ESD protective equipment and materials.
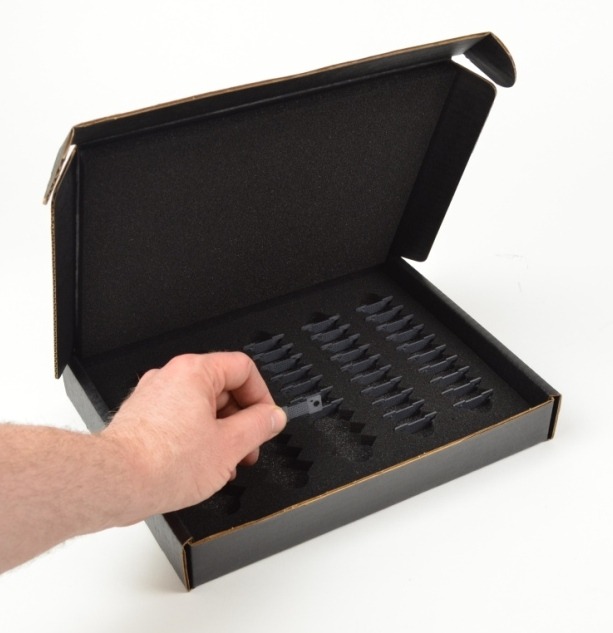
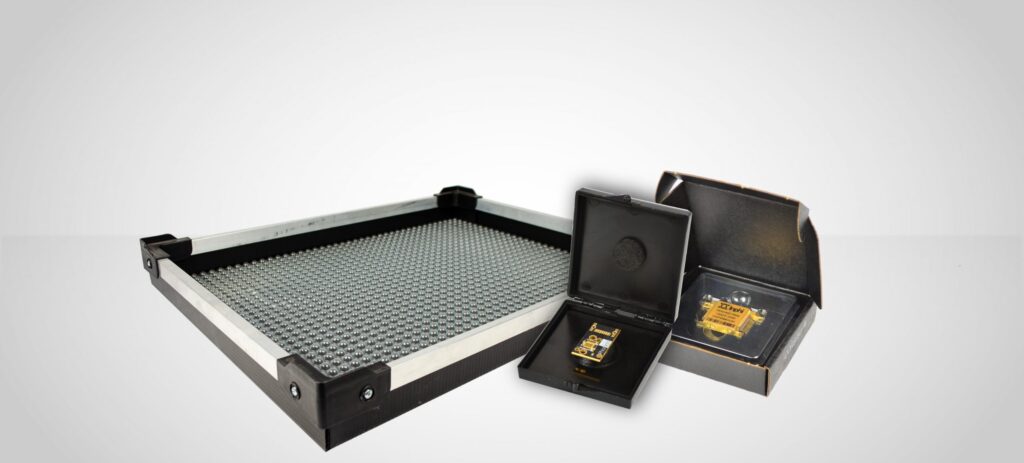
Package Compliance Verification
Periodically verify packaging materials as recommended in ANSI/ESD S541 (Packaging Materials for ESD Sensitive Items). Due to the large variety of packaging materials in use, the users should create their own compliance verification plan for packaging.
FOD (Foreign Object Debris)
One more item for your consideration in the use of foam for intimate contact with electronics is concerns of FOD – foreign object debris. All foams, regular non-ESD foams, antistatic foams, and conductive foams will shed particulates to varying degrees. Some are much better than others, but foams will generate some FOD. If you’re wondering about FOD when handling devices, select alternate options to avoid contact with foam.
Summary
So here we are. We have learned that you might have problems if you are using Pink ESD Foam.
- Pink ESD Foam has a shelf life
- The shelf life of that foam varies
- When it loses its ESD properties, it's unacceptable in, and potentially out, of an EPA
- If you're using Pink ESD Foam, it should be a short term solution
- Consider the potential FOD issues with foam
- Have a quality program in place if you are going to use foam long term
Thanks to the ESD Association, we have a potential solution to the challenge of limited shelf life. Compliance verification can make an antistatic foam viable. Without compliance verification, or if it's not practical, then other more permanent options should be chosen.